fechados por mês
eventos do CanalEnergia
mantenha-se informado
sobre o setor de energia.
No intuito de estimar a quantidade de motores elétricos reformados ou recondicionados presentes no mercado nacional, bem como o balanço de perdas para quem utiliza esses processos e seus respectivos materiais, o Instituto Brasileiro do Cobre (Procobre) encomendou uma pesquisa junto a PUC-Rio para avaliar e entender melhor a configuração desse negócio, numa relação direta com a portaria interministerial nº 29, de 26 de janeiro de 2017, que entrou em vigor no último sábado, 31 de agosto, determinando pela primeira vez na história níveis de eficiência mínimos para equipamentos elétricos trifásicos recondicionados, o que promete mexer com a indústria de fabricantes. Antes a exigência valia apenas para modelos novos.
A pesquisa aconteceu no âmbito do Comitê Gestor de Indicadores de Eficiência Energética (CGIEE) do Grupo de Trabalho do Ministério de Minas e Energia (MME), que está realizando a confecção de normas e levantamento de mercado para entender mais sobre os serviços de reparo de motores e repasse dessas peças reformadas que voltam à atividade nas indústrias em diversos usos, desde ventiladores a bombas hidráulicas, e que são responsáveis por 25% de toda a energia consumida no país. Já o Programa Nacional de Conservação de Energia Elétrica (Procel) estima que 2/3 do consumo da indústria de eletricidade seja por conta desses itens, mostrando ser uma parcela significativa dentro do segmento.
O estudo contemplou cinco estados – Rio de Janeiro, São Paulo, Minas Gerais, Rio Grande do Sul e Bahia – e 40 retíficas selecionadas por amostragem, e afirma que 90% do parque fabril no país é composto por máquinas retificadas, somando pouco mais de 20 milhões de unidades, enquanto que os motores novos produzidos no país chegam a pouco mais de 2 milhões, ou 10,6%. Em um levantamento inicial, realizado entre 2012 e 2013, a PUC-Rio e o Procobre já haviam constatado uma queda acentuada no mercado de motores novos em relação aos recondicionados, representando na época uma perda de eficiência energética de 7 TWh para o país. Já nesse ano o cenário piorou consideravelmente.
“Passados pouco mais de quatro anos, a perda energética cresceu quase 20%, chegando a 8,43 TWh ao ano, o que seria suficiente para abastecer 4,5 milhões de moradias. Para os empresários, donos de indústrias, esse montante de energia ao custo total das tarifas aplicadas pelas distribuidoras equivaleria a uma perda de R$ 4,5 bilhões”, enfatiza Glycon Garcia Jr, diretor-executivo do Procobre.
Na parte que considera o potencial de máquinas obsoletas já terem passado por alguma reforma durante sua vida útil, o prejuízo observado chega a R$ 480 milhões na análise anual e está relacionado ao fato de tais equipamentos não cumprirem os índices mínimos de eficiência definidos pela Portaria nº 488 do Inmetro de 08/12/2010, que trata do funcionamento e do gasto energético adequados dessas máquinas. A pesquisa também aferiu que a cada recondicionamento de um mesmo motor ocorre a perda de 2% do seu rendimento e que o total de peças reformadas é responsável por 2,8% da emissão de gases de efeito estufa (GEE) liberados na atmosfera só no Brasil. Outro resultado mostra que a cada 1% de perda de energia evitada geraria uma economia R$ 16,2 milhões em investimentos de expansão pelas concessionárias.
Economia que não se justifica
Segundo o Diretor do Procobre, o Instituto tem interesse particular em trabalhar no desenvolvimento de ideias onde o cobre possa ser melhor utilizado, sendo a eficiência energética uma área importante nesse quesito. No caso, muitos dos motores são recauchutados com materiais mais baratos e menos eficientes, como o alumínio e em alguns casos até sucata. “São soluções por economia, mas que saem caro a médio e longo prazo. Compram gato por lebre” comenta o executivo, destacando que todas literaturas técnicas apontam que durante a vida útil de um motor o custo com energia chega a representar 95% do gasto dispendido com esses equipamentos.
Glycon explica que um motor mal reformado consome tanta energia que não justifica o preço inferior pago nele e que o gasto energético é um absurdo quando comparado a um modelo premium IR3 ou das versões americanas ou europeias, com níveis de eficiência elevadíssimos. “O que a portaria coloca é para alcançarmos esse patamar”, resume. Na sua visão, a nova legislação é fundamental, um grande passo na direção da economia de energia e um melhor direcionamento de investimentos futuros para o país. “O Brasil vai economizar muito em energia, deixando de precisar investir em novas usinas”, completa.
A previsão do MME é que a nova determinação de rendimento para máquinas de indução trifásica gere uma economia acumulada de 11.213 GWh no período de 2019 a 2030, atingindo em 2030 a economia de 1.830 GWh ao ano, equivalente ao atendimento de mais de 560 mil residências em um ano ou ao consumo de uma cidade de quase 1,9 milhão de pessoas. Além disso, a pasta entende que os índices de conformidade também promovem a melhoria da segurança média destes produtos no mercado.
Motores rebubinados são comercializados em SP. Valor pode chegar a 50% de um modelo novo mas consumo excessivo da máquina não justifica economia no preço para os clientes (foto Hp Elétrica)
Na avaliação do Professor do Programa de Pós-Graduação em Metrologia da PUC-Rio, Rodrigo Calili, que liderou o estudo pela Universidade, a norma fará com que fabricantes e clientes primem mais pela qualidade e eficiência em relação ao custo do equipamento, que pode chegar a metade do valor de um novo. Ele conta que há motores que estão há 15 anos no mercado, muito defasados, e que a principal pretensão é mudar a prática do mercado e reduzir o número de peças recondicionadas que voltam a ser comercializadas, além de incentivar a troca de modelos antigos IR2 por outros novos. “Muitas empresas que fazem o serviço também vendem”, lembra o professor.
Calili ressalta que em tese o mercado nem poderia comercializar esses equipamentos reformados, mas a prática acontece geralmente em empresas pequenas, por escassez de recursos e falta de preocupação com a eficientização, pensando mais no bolso e ao curto prazo da linha de produção. “Num país onde as tarifas são das mais caras do mundo e num setor onde um dos maiores custos é a eletricidade, as empresas que pensam em eficiência energética tornam-se mais competitivas”, sustenta o professor, afirmando que, ainda que à primeira vista o preço mais barato seja mais atrativo, os motores obsoletos possuem a produtividade comprometida, vida útil curtíssima e consumo energético excessivo, o que acaba encarecendo o motor reformado. “Empresas recondicionam motores sem condições de uso, muitas vezes adquiridos como sucata, e que nunca deveriam voltar ao mercado”, afirma.
Ao disponibilizar informações sobre o recondicionamento e o desperdício de energia representado por esses processos, a pesquisa busca oferecer ao empresariado a possibilidade de ponderar mais precisamente quanto a relação custo x benefício de aquisição de equipamentos reformados em relação a novos. Já para o poder público, os dados podem servir para subsidiar políticas de incentivo para a troca dessas peças e a definição, inclusive, de um número limite de arranjos, além de ser um instrumento para adoção de medidas de fiscalização junto às retíficas, com foco na melhoria do serviço oferecido.
Propostas e melhorias
Na visão do especialista o estudo é pertinente para reavaliar os números aferidos em 2012, através de uma metodologia mais robusta e muito mais criteriosa que a edição anterior, sendo considerado um trabalho chave para analisar os rumos do mercado com a nova legislação. “Pretendemos melhorar ainda mais a parte de medição das informações na próxima pesquisa. Muitos dos dados que usamos vem da literatura”, afirma Rodrigo, contando que nesta edição foram elencados 15 indicadores para levantar e estimar as chamadas perdas normais no motor em relação as perdas de fabricação, potencializando essa medição para saber especificamente o quanto cada parte desses processos mapeados apresentam em perdas.
A avaliação recente também traz o relato de pessoas que trabalharam com motores reformados, que atestaram a baixa qualidade dos equipamentos. Mas um ponto ressaltado pelos pesquisadores foi o desconhecimento técnico de muitos profissionais quanto aos procedimentos corretos para os rebobinamentos. Para tanto, uma das propostas que deriva do levantamento é aumentar o número e qualidade dos cursos profissionalizantes e de treinamentos no Brasil.
“Tentamos uma aproximação com a Abraman, mas não obtivemos sucesso no âmbito do GT, mas o Senai e o Senac, através do Grupo S, tem sido um parceiro efetivo”, conta o professor, afirmando ter sido definido também o que um curso básico para o processo exige. Já uma iniciativa que toma corpo dentro do Grupo de Trabalho do Ministério é a promoção de palestras pelo país, já realizadas em São Paulo e no Rio de Janeiro com apoio da agência Alemã GIZ, no intuito de levar o conhecimento dessa nova legislação à sociedade.
Há mais ações em andamento nesse sentido, como o projeto da Norma Brasileira de Reparos de Motores de Uso Geral para regulamentar os serviços de retífica, além de workshops para conscientizar setores envolvidos, inclusão do tema nos projetos do Procel, criação de um curso no Senai sobre reparos dessas máquinas e a elaboração de uma cartilha de orientação para o usuário final e com informações e medidas educativas para a população.
Outro ponto que chamou a atenção dos especialistas e que não tinha aparecido anteriormente é a quantidade de motores importados que começaram a entrar no país, muitos de má qualidade e por vezes enrolados com alumínio ao invés de cobre. Foi proposto então uma alteração dos códigos de importação para que esses produtos passem por testes em laboratórios aqui no Brasil, antes de ir para o mercado. “A ideia é reduzir a entrada desses motores no país”, resume Calili.
Rodrigo Calili: pretensão da portaria é mudar prática do mercado e reduzir o número de peças reformadas que voltam a ser comercializadas (foto: PUC-Rio)
Nova lei exige fiscalização
Como toda lei que nasce no país, um dos desafios é o seu cumprimento por parte do setor produtivo e dos consumidores finais, o que exige fiscalização dos órgãos competentes. A portaria que entrou em vigor indica que caberá ao Inmetro esse papel, inclusive com a competência de definir medidas regulatórios para as inspeções.
Rodrigo Calili diz ainda não saber ainda como o Instituto fará a fiscalização, sobretudo por que do ponto de vista prático, o órgão normativo conta com cada vez menos colaboradores trabalhando. “Não adianta ter a norma sem fiscalização efetiva. A gente conhece o Brasil e se não tiver isso, sinceramente, é utópico pensar que isso vá para frente”, comenta.
Como ponto positivo, o pesquisador revela que tem enxergado em várias empresas o interesse em participar dos workshops que estão sendo promovidos, mostrando que há uma preocupação de fato em atender o que a nova lei está colocando. “Já estimamos payback de dois anos em motores que são utilizados constantemente durante todos os dias. O volume de motores recondicionados tende a cair”, pontua o professor.
Fabricantes se adaptam
A medida é aplicável para o comércio de motores novos e recondicionados, utilizados em 537 mil unidades industriais em funcionamento no país, num setor que responde por cerca de 41% no consumo de energia elétrica no Brasil, como estima a Confederação Nacional da Indústria (CNI). Segundo números da entidade, em linhas gerais, esses motores são responsáveis por 68% do consumo energético nas empresas e aproximadamente 30% dessas máquinas possuem mais de 20 anos de uso. Já em uma análise de possíveis resultados, a modernização desses sistemas permitirá a redução do consumo em até 60%, sendo que 27% de toda eletricidade consumida no país está relacionada aos motores elétricos.
Na visão de Leandro Bertolino, Gerente de Engenharia da Hércules Motores Elétricos, o que se percebe entre os fabricantes do setor é que falta ainda bastante informação do mercado referente a questões dessa migração do modelo IR2 para o IR3, principalmente por ser um segmento produtivo que se atém muito a questões de custo do motor. Segundo ele, é inevitável que não haja um aumento no preço a ser repassado ao consumidor, devido a utilização de uma quantidade maior de material ativo e de maior qualidade, como cobre e chapas metálicas.
“O que está sendo divulgados por nós e acredito que pelos concorrentes é de que haverá um acréscimo no valor final do produto”, confirma o executivo, sem revelar números. Para ele o que acontece hoje no mercado é que as empresas pegam motores antigos, de dez anos e conferem uma pintura, trocam algum rolamento e colocam de novo para o mercado. “Como o Inmetro irá fiscalizar isso eu ainda não sei. Mas esse aumento nada mais é do que para atender a portaria”, pondera o gerente.
Leandro conta que a companhia teve de empreender investimentos de aproximadamente R$ 5 milhões para fazer a adequação da linha de motores da empresa à portaria. “Não é só colocar mais cobre ou chapa, mas pensar em todo desenho da lâmina, eficiência, com o menor impacto no custo final para ficar competitivo no mercado”, explica.
A partir de 1º de setembro a fábrica da empresa em Timbó, cerca de 20 Km de Blumenau, Santa Catarina, e qualquer outra no Brasil só poderá produzir motores IR3, estes no caso principalmente utilizados para lavadoras de roupa e fogões, produtos comercializados pelo Grupo Miller, que controla a Hércules. “Já temos alguns modelos de IR3 sendo comercializados, mas a linha completa só será disponibilizada a partir de 1º de setembro”, assegura o executivo.
“Tivemos que realizar uma série de estudos técnicos e econômicos e investimentos em máquinas de última geração para conseguir entregar um produto com um custo benefício melhor que meu concorrente”, revela Bertolino, lembrando que o trabalho veio sendo desenvolvido nos últimos dois anos, desde quando a medida foi anunciada em 2017. “Preciso saber se o torque e a eficiência está atendendo a norma, o que exige investimentos em dinamômetros e outros equipamentos”, complementa.
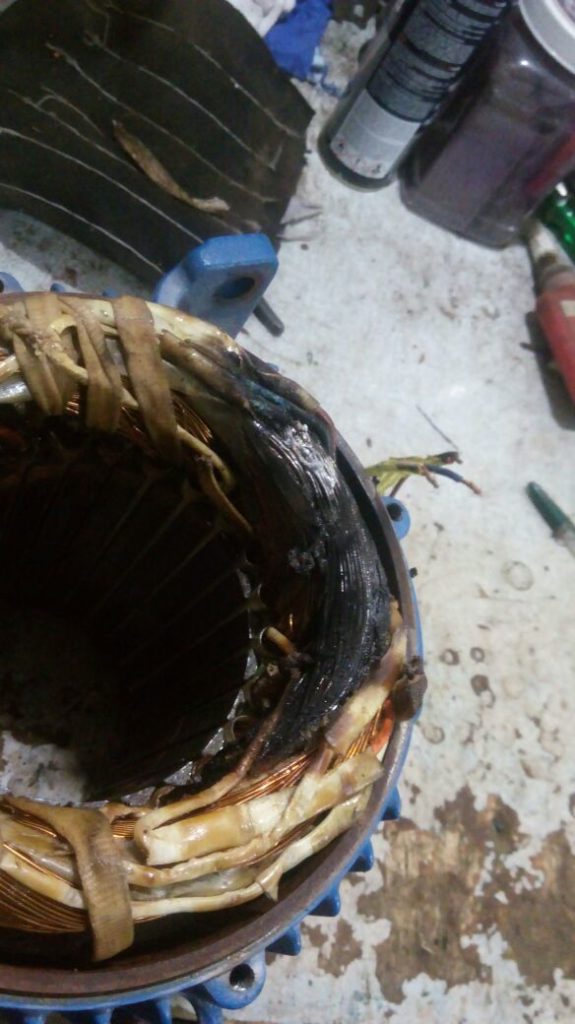
Sobre a fiscalização da nova lei, o gerente entende que será um trabalho grande para o Inmetro e que não está claro também para os fabricantes de como isso será feito. “Para fazer um rebobinamento de um IR3, tem que haver uma forma de comprovar que o trabalho que está sendo executado está atingindo os níveis de eficiência exigidos”, aponta. Segundo ele, a empresa vem divulgando todo conhecimento e aparato técnico para seus colaboradores espalhados pelo Brasil, inclusive com treinamentos in loco para os atendentes nos postos de trabalho. “Boas práticas para o processo, sempre olhando para os dados do fabricante, cada um com seus dados elétricos específicos”, delimita.
Por sua vez, a Weg, uma das líderes no segmento no país, afirmou em nota que ao longo de sua trajetória sempre teve a preocupação em minimizar os custos operacionais na indústria, lançando motores elétricos com rendimentos acima dos padrões de mercado desde a década de 1990, e disponibilizando atualmente modelos IR4 Super Premium e IR5 Ultra Premium.
A fabricante também oferece o See+, um software gratuito para simulação da aplicação de motores elétricos de alta eficiência com foco na redução do consumo de energia elétrica na indústria. O sistema é multiplataforma, sendo disponível para computador, tablet ou celular, e gera relatórios completos de viabilidade de troca de um ou mais motores elétricos.
O programa calcula o potencial de economia que o usuário pode obter com a substituição de um equipamento em operação, queimado ou novo, por um de maior eficiência, através de dados do motor atual ou a ser adquirido como potência, número de polos, número de rebobinagens, quantidade e horas trabalhadas.
Como os motores elétricos são responsáveis por boa parte da demanda elétrica no país e no mundo, a redução desse consumo trará inevitavelmente inúmeros benefícios, não somente para a natureza, mas para a sociedade e toda a geração futura. Sendo assim, a economia energética resultará, de forma direta e indireta, na redução do uso de recursos naturais e da emissão de poluentes ao meio-ambiente.